TC4鈦合金由于其輕量化和高性能的特性,被廣泛用于汽車關鍵零部件中,以提升車輛的性能和燃油經濟性。TC4鈦合金材料本身的物理和化學特性,在加工過程中易產生過熱、磨損和變形等問題,在此情況下需要優(yōu)化加工工藝參數和采用先進的制造技術,以此來保證汽車制造質量。文章分析了TC4鈦合金的特性,提出了在TC4鈦合金加工中主要的工藝,針對汽車制造過程中常見的關鍵部件,具體分析了TC4鈦合金的應用情況,以此更好地理解和應用TC4鈦合金在汽車工業(yè)中的價值,旨在為汽車工業(yè)中材料和工藝的發(fā)展提供參考。
一、TC4鈦合金的基本特性
TC4鈦合金因其獨特的化學成分和出色的性能,在工業(yè)界尤其是汽車制造中獲得了廣泛應用,其主要成分包括90%的鈦、6%的鋁和4%的釩,這種特定的配比使其具備高強度、低密度和優(yōu)異的耐腐蝕性等特點。與傳統(tǒng)的鋼材和鋁合金相比,TC4鈦合金的密度僅為4.43g/cm3,大約是鋼的60%,因此在保持結構強度的同時能減輕重量,有利于提高車輛的燃油效率和動力性能。TC4鈦合金的機械性能也十分出色,其抗拉強度可達到900~1100MPa,具有良好的延展性和韌性,能承受較大的變形而不發(fā)生斷裂,這對汽車部件在復雜應力環(huán)境下的耐用性至關重要。其卓越的耐腐蝕性使其在各種惡劣環(huán)境下依然保持穩(wěn)定,特別適用于汽車的外部和內部關鍵部件,如發(fā)動機、車身框架和排氣系統(tǒng)等。這些優(yōu)異特性使TC4鈦合金成為汽車工業(yè)中不可或缺的高級材料,既能滿足現代汽車對輕量化和高性能的雙重需求,又能提升車輛的整體安全性和耐久性。
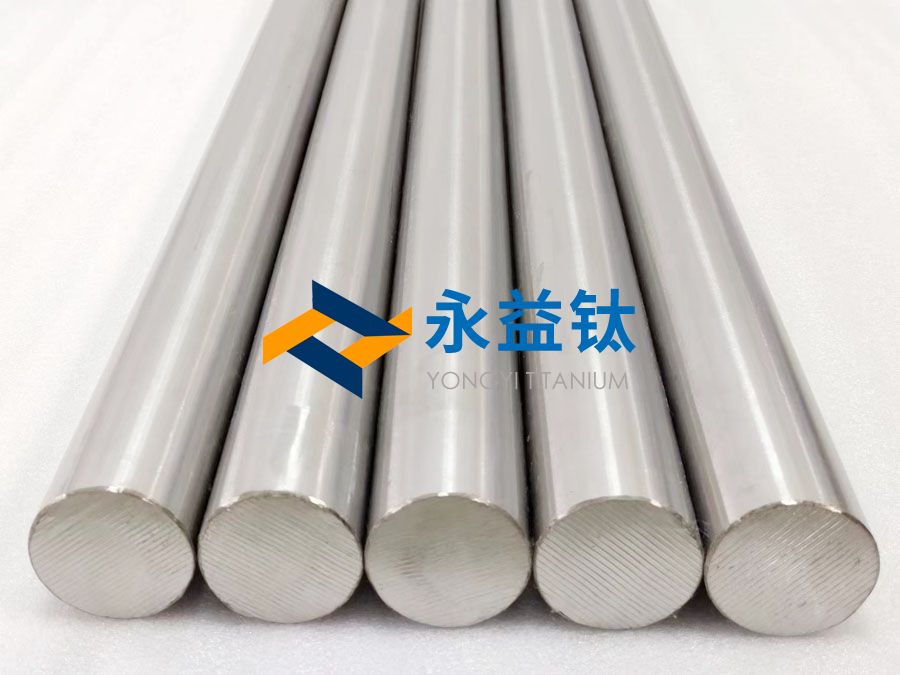
二、TC4鈦合金的加工工藝
(一)鍛造工藝
TC4鈦合金鍛造工藝包括熱鍛和冷鍛兩大類,其中熱鍛是最常用的工藝,在熱鍛過程中,TC4鈦合金通常被加熱到900℃~950℃的高溫,這一溫度范圍內材料處于高塑性狀態(tài),便于成型和變形,熱鍛可以提升合金的晶粒細化效果,使材料的強度和韌性得到提升,同時減少內部缺陷,如氣孔和微裂紋。冷鍛則在室溫或稍高于室溫的情況下進行,雖然冷鍛能提高材料的強度和表面光潔度,但由于TC4鈦合金本身的高硬度和高強度特性,冷鍛過程對設備和模具的要求較高,通常需要采用高強度的硬質合金模具,并且需要較高的加工壓力。為了獲得最佳的鍛造效果,通常需要結合有限元分析和實驗數據,優(yōu)化鍛造工藝參數,確保TC4鈦合金零部件在實際應用中的性能。
(二)鑄造工藝
鑄造工藝是加工TC4鈦合金的另一種重要方法,特別是在制造復雜形狀和大型零部件時展現出獨特優(yōu)勢。其中,真空鑄造通過在真空環(huán)境下進行,能有效避免鈦合金與空氣中的氧、氮等氣體發(fā)生反應,減少氣孔和夾雜物的產生,從而提高鑄件的純凈度和力學性能。精密鑄造工藝的采用則通過精密模具和先進的澆注技術,可以實現高精度和高復雜度零部件的制造,減少后續(xù)加工的工作量。由于TC4鈦合金的熔點較高,其鑄造過程需要采用耐高溫的陶瓷材料作為模具,并且要控制合適的冷卻速率,以防止鑄件產生裂紋和變形。在鑄造過程中,流動性和填充能力是影響最終鑄件質量的重要因素,通過優(yōu)化鑄造溫度、澆注速度和模具設計,可以提高鑄件的致密度和表面質量。在汽車工業(yè)中,TC4鈦合金鑄造件廣泛應用于發(fā)動機渦輪、閥門和懸掛系統(tǒng)等關鍵部件,為汽車的輕量化和高性能提供了重要支撐。
(三)切削加工
在TC4鈦合金加工過程中,切削加工是去除多余材料來獲得所需的零部件形狀和尺寸,鈦合金在切削過程中容易產生高溫,這不僅加速了刀具的磨損,還可能導致工件表面出現燒傷或硬化現象。為了解決這一問題,選擇合適的刀具材料和優(yōu)化切削參數顯得尤為重要。通常采用硬質合金或陶瓷刀具,因為其具有較高的耐熱性和耐磨性。在加工過程中,需要控制切削速度、進給量和切削深度,較低的切削速度和適中的進給量可以有效降低切削溫度,延長刀具壽命,同時保證工件的表面質量。使用高效冷卻液不僅能帶走切削熱,還能潤滑刀具與工件接觸面,減少摩擦和磨損,從而提高加工效率和質量。在切削加工過程中,還需要特別關注加工變形和殘余應力問題,優(yōu)化加工路徑和切削順序,最大限度地減少工件的熱變形和內應力。
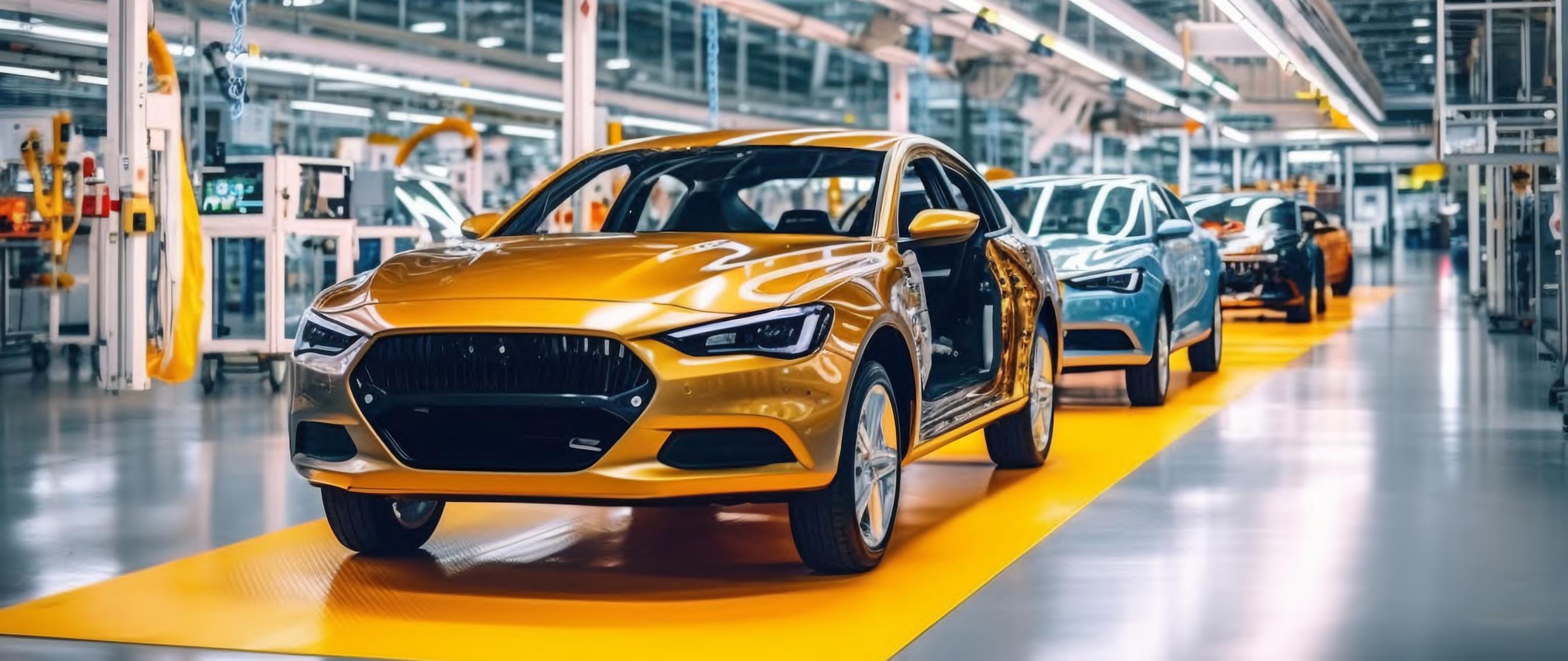
(四)焊接工藝
TC4鈦合金加工中焊接能連接不同零部件,形成復雜的結構,焊接TC4鈦合金具有較高的技術難度,主要因為鈦合金在高溫下極易與氧、氮和氫等氣體發(fā)生反應,導致焊接區(qū)域產生脆性相和氣孔,從而影響接頭的強度和韌性。為了確保焊接質量,常采用鎢極惰性氣體保護焊(TIG焊)和激光焊等先進焊接工藝。TIG焊使用惰性氣體,如氬氣作為保護氣體,可以有效防止高溫焊接區(qū)域與空氣接觸,減少氧化和污染。TIG焊對焊接環(huán)境要求嚴格,必須在潔凈、無塵的條件下進行,并且需要高度熟練的操作人員。激光焊則利用高能量激光束進行焊接,具有熱影響區(qū)小、焊接速度快和變形小等優(yōu)點,適用于精密和復雜結構的焊接。在進行TC4鈦合金加工中,焊接工藝參數的優(yōu)化同樣重要,如焊接電流、焊接速度、保護氣體流量等都會直接影響焊接質量,焊接速度需要適中,確保焊縫成形良好,并避免過熱或未焊透。在保護氣體的選擇和流量控制方面,確保充足且均勻的氣體覆蓋,防止氧化和污染。
三、TC4鈦合金在汽車工業(yè)中的應用
(一)在發(fā)動機部件中的應用
在汽車工業(yè)中,由于發(fā)動機在工作時需承受高溫、高壓和高速運動,因此對材料的性能要求極為苛刻。TC4鈦合金以其優(yōu)異的高強度、低密度和耐高溫性能,成為發(fā)動機部件的理想材料。在發(fā)動機部件中,活塞需要在高溫高壓環(huán)境下頻繁往復運動,使用TC4鈦合金制成的活塞不僅能減輕重量,提高發(fā)動機的功率重量比,還能有效降低活塞的慣性力,減少機械磨損,延長發(fā)動機壽命。連桿作為連接活塞和曲軸的關鍵部件,其強度和韌性直接影響發(fā)動機的可靠性。TC4鈦合金連桿由于其高強度和抗疲勞性能,能承受劇烈的工作環(huán)境,減少斷裂和故障風險。進氣閥則需要具備良好的耐磨性和耐高溫氧化性能,TC4鈦合金在這方面表現出色,能在高溫高壓的燃燒室環(huán)境中長期保持穩(wěn)定的性能,不易變形和氧化。TC4鈦合金的優(yōu)良熱導性有助于提高發(fā)動機的熱效率,減少燃油消耗。TC4鈦合金在發(fā)動機部件中的應用,不僅提高了發(fā)動機的整體性能和可靠性,還推動了汽車工業(yè)向輕量化和高效能方向的發(fā)展。
例如,某汽車制造廠在鍛造汽車發(fā)動機連桿中選擇采用TC4鈦合金,在制造時,初始鍛造溫度設置為940℃,變形速率控制在0.01~0.1s-1,通過多次鍛壓成形,最終連桿的晶粒尺寸可以控制在10~15μm,確保材料具有優(yōu)良的力學性能。鍛造完成后,連桿需要進行熱處理,以消除內應力并優(yōu)化材料性能。在此次加工中采用雙重退火工藝,第一階段在700℃進行退火2h,然后緩慢降溫到室溫;第二階段在550℃進行退火4h,然后隨爐冷卻,經過這樣的熱處理,TC4鈦合金連桿的屈服強度可以達到850MPa,伸長率超過10%。鍛造和熱處理后的連桿需要進行精密機加工來達到設計的尺寸和公差要求,由于TC4鈦合金的硬度較高,機加工難度較大,因此該制造廠采用高性能刀具和優(yōu)化的切削參數。
使用硬質合金刀具時,切削速度為30~50m/min,進給率為0.05~0.15mm/rev。對于較大直徑的孔加工,采用鉆削和鉸削結合的工藝,鉆削速度控制在20~30m/min,進給率為0.05~0.1mm/rev。在加工過程中使用水基冷卻液,冷卻液流量控制在10~20L/min。加工完成后,對連桿進行機械性能檢測,檢測項目包括抗拉強度、屈服強度、延伸率和疲勞性能。實際檢測結果顯示,TC4鈦合金連桿的抗拉強度為950MPa,屈服強度為860MPa,延伸率為12%,疲勞壽命超過106次循環(huán)。
(二)在車身結構中的應用
TC4鈦合金在車身結構中的應用主要體現在車身框架和防撞梁等關鍵部件上,車身框架是車輛的骨架,其強度和剛性直接關系到整車的安全性能和操控穩(wěn)定性。使用TC4鈦合金制造車身框架,可以減輕車身重量,從而提高燃油效率和車輛加速性能。同時,TC4鈦合金具有出色的耐腐蝕性和長久的使用壽命,能在惡劣環(huán)境中保持結構完整,減少車身部件的維修和更換頻率。防撞梁是車身結構中的另一重要部分,主要負責吸收碰撞能量,保護乘員安全,而TC4鈦合金的高強度和高韌性特性使防撞梁能在碰撞時有效吸收和分散沖擊力,減少車身變形,提升車內乘員的安全性。TC4鈦合金的高能量吸收效率使其能在較小的形變范圍內承受巨大的沖擊力,這對現代汽車設計中的輕量化和高強度要求尤為重要。
以某高端電動汽車品牌的旗艦車型為例,該車型在車身結構中廣泛采用了TC4鈦合金,提升了整車的性能和安全性。該車型的車身框架部分采用了TC4鈦合金,使用了熱鍛和真空鑄造相結合的工藝。在制造過程中,車身框架的關鍵節(jié)點采用熱鍛工藝處理,通過在900~950℃的高溫下鍛造TC4鈦合金,使其內部的晶粒結構得到細化,提升了材料的力學性能。經過熱鍛處理的TC4鈦合金框架部分,其抗拉強度達到了1050MPa,比傳統(tǒng)鋼制框架提高了約30%。同時,整車的重量顯著降低,達到了車身減重150kg的效果,從而提升了電動車的續(xù)航里程和加速性能。在車身框架的熱鍛過程中,鍛造壓力控制在1500~2000t,確保了鈦合金的充分塑性變形和內部缺陷的減少,防撞梁的精密鑄造則在真空度為10-5Pa的條件下進行澆鑄,保證了鑄件的致密性和力學性能。應用這些先進工藝,該車型的整體車身剛性提高了20%,而整車重量卻降低了約10%,實現了輕量化和高強度的完美結合。
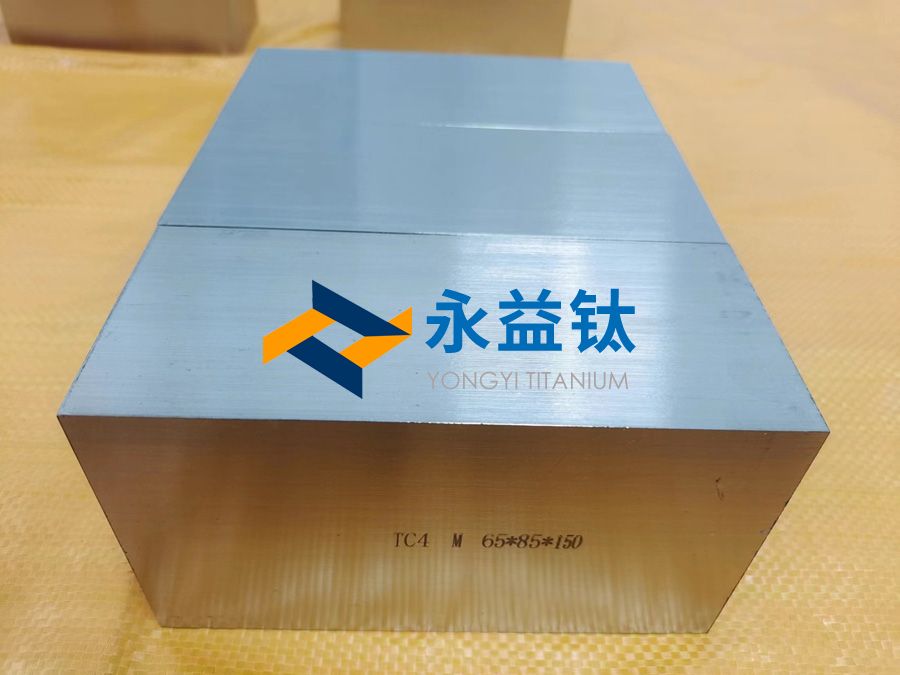
(三)在懸掛系統(tǒng)中的應用
懸掛系統(tǒng)是汽車行駛平穩(wěn)性和操控性能的核心,其性能直接影響車輛的舒適度和安全性。TC4鈦合金的低密度和高強度使懸掛系統(tǒng)中減震器和彈簧能在保證強度的前提下減輕重量,這不僅有助于提高車輛的燃油效率,還能降低簧下質量,從而提高車輛的操控性能和舒適度。減震器需要在各種復雜路況下有效吸收和緩解沖擊力,使用TC4鈦合金制造的減震器具有更高的耐疲勞性和耐腐蝕性,能在長時間的使用中保持穩(wěn)定的性能,減少維護成本和頻率。彈簧作為懸掛系統(tǒng)中的關鍵彈性元件,采用TC4鈦合金彈簧進行制造,不僅具有高彈性模量和良好的回彈性,還能在高載荷下保持穩(wěn)定的彈性變形,提供更好的支撐力和減震效果。
舉例來說,某高性能跑車為了提高車輛的操控性和舒適性,決定在其懸掛系統(tǒng)中應用TC4鈦合金。工程師根據懸掛系統(tǒng)的應力分析和性能需求,設計了采用TC4鈦合金制造的控制臂和連桿,初步設計階段通過計算機輔助設計(computer aided design,CAD)和有限元分析(finite element analysis,FEA)驗證了設計的可行性和材料性能。為了確保TC4鈦合金的微觀結構和機械性能,在鍛造過程中嚴格控制溫度,TC4鈦合金的鍛造溫度范圍為950℃~1100℃,實際操作中采用了1050℃的鍛造溫度。之后采用數控鍛壓機進行鍛造,精確控制壓力和速度,通過熱等靜壓(HIP)工藝消除內部缺陷,提高材料致密性。在熱處理中,950℃進行固溶處理1h,然后迅速冷卻至室溫,這一步驟可以增強材料的韌性和塑性,在550℃進行時效處理6h,提高材料的強度和硬度。
在鍛造完成后,使用數控機床對鍛造后的鈦合金零件進行精密加工,在加工過程中使用了冷卻潤滑液來防止加工熱引起的表面氧化。同時,采用化學拋光和陽極氧化工藝,提高表面光潔度和耐腐蝕性能,陽極氧化后,表面形成了一層致密的氧化膜,厚度約為5~10μm。隨后,將加工好的鈦合金零件裝配到懸掛系統(tǒng)中,并進行整車道路測試,測試結果顯示,整車減重約15kg,懸掛系統(tǒng)的響應速度和操控性能明顯提升。
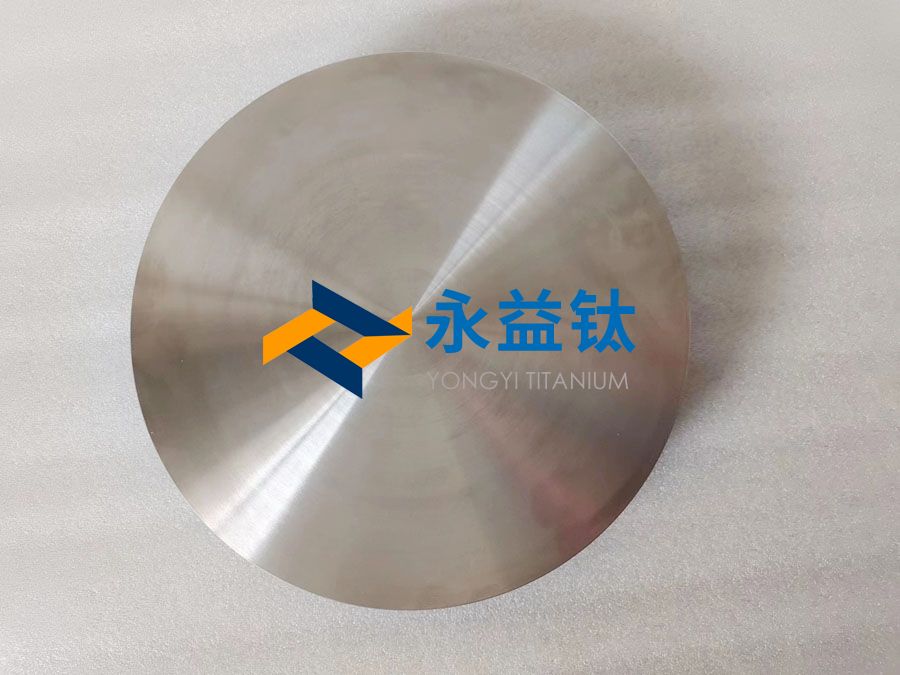
隨著新能源汽車和高性能車輛的發(fā)展,對輕量化和高強度材料的需求不斷增加。在加工工藝進步和成本減少的背景下,TC4鈦合金在汽車工業(yè)中的應用將進一步擴大,推動整個行業(yè)向更高效、更環(huán)保的方向發(fā)展。因此,深入研究TC4鈦合金加工工藝不僅有助于解決其在加工中的技術挑戰(zhàn),還能推動汽車工業(yè)的技術進步和產品創(chuàng)新。
作者/李楠林
單位哈爾濱東安高精管軸制造有限公司
相關鏈接