鈦合金具有高比強(qiáng)度、耐高溫、耐腐蝕等優(yōu)異的性能,已廣泛應(yīng)用于航空航天、兵器、汽車、能源、生物醫(yī)療及體育用品等領(lǐng)域[1-2]。超聲波檢測(cè)作為一種重要的無(wú)損檢測(cè)手段,廣泛應(yīng)用于鈦合金產(chǎn)品的生產(chǎn)和檢驗(yàn),相關(guān)國(guó)標(biāo)和國(guó)軍標(biāo)中都規(guī)定了超聲波檢測(cè)要求。除了對(duì)單體缺陷和連續(xù)缺陷的尺寸進(jìn)行限制,對(duì)鈦合金超聲波底波衰減也進(jìn)行了明確規(guī)定。特別是要求較高的軍用產(chǎn)品,對(duì)超聲波雜波水平也提出了很高的要求。例如,在GJB494A—2008《航空發(fā)動(dòng)機(jī)壓氣機(jī)葉片用鈦合金棒材規(guī)范》中,要求靜子葉片用小規(guī)格棒材(φ≤45mm)的超聲波檢測(cè)雜波水平不大于φ0.8-9dB,轉(zhuǎn)子葉片用棒材雜波水平不大于φ0.8-12dB。
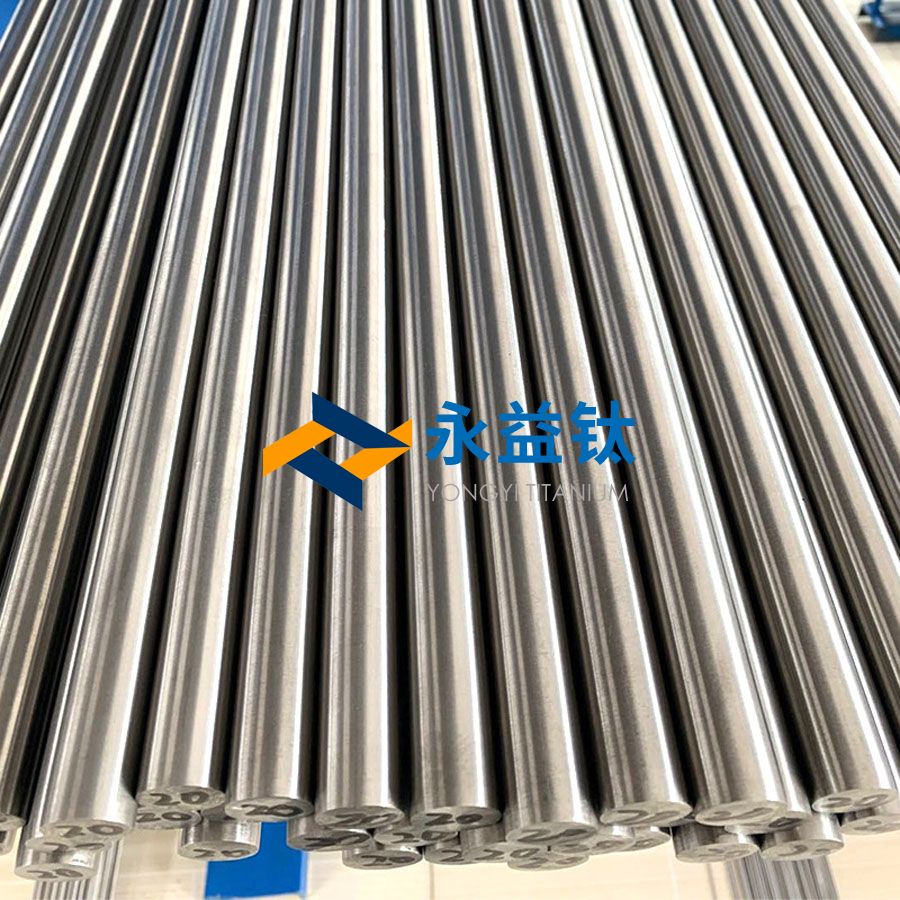
在生物醫(yī)療領(lǐng)域,醫(yī)用鈦合金超聲刀廣泛應(yīng)用于外科手術(shù)。超聲刀的超聲波波速不僅需要控制在一定范圍,而且波速波動(dòng)值越小越好[3-4]。
然而,鈦合金產(chǎn)品由于成分和加工工藝的差異,其微觀組織千差萬(wàn)別。復(fù)雜的多相多晶結(jié)構(gòu),以及晶粒取向的差異性,導(dǎo)致不同鈦合金產(chǎn)品的超聲行為截然不同。影響鈦合金產(chǎn)品超聲波信號(hào)的因素包括超聲檢測(cè)方法(接觸法、水浸法等),超聲波探頭頻率,鈦合金的表面粗糙度、顯微組織類型、晶粒尺寸和形狀、織構(gòu)類型和強(qiáng)度、殘余應(yīng)力等[5-14]。然而,鈦合金產(chǎn)品在冷熱加工過(guò)程中,無(wú)法滿足各部位的均勻變形,這也造成了鈦合金產(chǎn)品不同部位的組織和織構(gòu)存在差異。因此,當(dāng)超聲波檢測(cè)時(shí)出現(xiàn)雜波水平增大、底波強(qiáng)度衰減等異常信號(hào)時(shí),判定其準(zhǔn)確來(lái)源存在一定的難度。
為了深入研究鈦合金組織和織構(gòu)對(duì)超聲波檢測(cè)信號(hào)的影響,科研人員排除硬件設(shè)備、表面粗糙度、內(nèi)部缺陷的干擾,對(duì)超聲信號(hào)異常區(qū)域進(jìn)行組織和織構(gòu)分析[5-9]。本文介紹了超聲波在鈦合金中的傳播、反射和衰減行為,針對(duì)超聲波波速變化、底波衰減、雜波水平3種常見的超聲波檢測(cè)信號(hào),詳細(xì)論述了鈦合金組織和織構(gòu)對(duì)超聲波影響的規(guī)律和機(jī)理。
1、鈦合金中超聲波波速的影響因素
超聲波的波速與介質(zhì)的彈性模量和密度密切相關(guān)。由于鈦的晶體結(jié)構(gòu)為密排六方結(jié)構(gòu),當(dāng)超聲波在鈦合金中傳播時(shí),其傳播速度會(huì)受到彈性模量各向異性的影響。對(duì)于鈦單晶,密度為ρ=4.507g/cm3,彈性模量張量的分量分別為


超聲波在鈦單晶中的縱波波速分別為:
c 軸方向
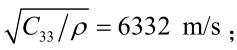
垂直于c軸方向

由此可見,超聲波在不同取向的鈦晶粒中傳播速率不同,理論波速差高達(dá)329m/s[9]。
對(duì)于多晶鈦材料中的超聲波波速,不僅需要考慮彈性模量各向異性的影響,還需要考慮材料宏觀織構(gòu)的影響。
Zheng等人[16]表征了φ260mm大規(guī)格Ti6242s合金棒材的組織和織構(gòu),并對(duì)棒材橫截面進(jìn)行水浸超聲波波速檢測(cè),計(jì)算了沿直徑方向的波速數(shù)據(jù)。
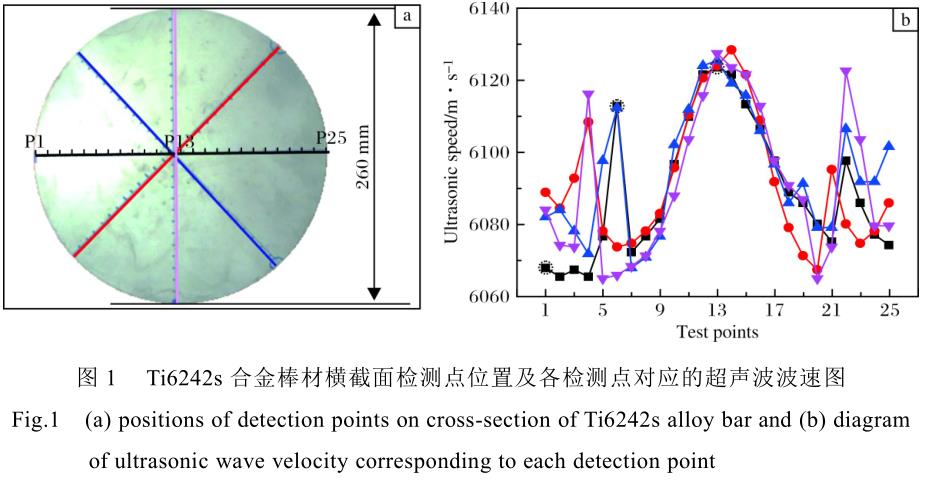
圖1a展示了超聲檢測(cè)樣品和檢測(cè)點(diǎn),沿直徑方向每間隔1cm取一個(gè)檢測(cè)點(diǎn),在每條直徑上取25個(gè)檢測(cè)點(diǎn),沿4個(gè)直徑方向呈“米”形進(jìn)行超聲波波速檢測(cè)。圖4b展示了4個(gè)方向上各檢測(cè)點(diǎn)的超聲波波速數(shù)據(jù),4條曲線顯示出相同的變化趨勢(shì)。棒材邊部檢測(cè)點(diǎn)(P1-3;P23-25)波速較低,接著波速會(huì)出現(xiàn)一次突然起落變化,然后逐漸增加,在棒材中心位置(P13)達(dá)到最大值。圖1b中波速低值和高值的特征點(diǎn)位(圖中黑色圓圈檢測(cè)點(diǎn))分別對(duì)應(yīng)圖1a中樣品直徑方向黑色線上的檢測(cè)點(diǎn)P1、P6、P7、P13,對(duì)其進(jìn)行XRD宏觀織構(gòu)檢測(cè),各檢測(cè)點(diǎn)(002)晶面的極圖數(shù)據(jù)如圖2所示。P1和P7檢測(cè)點(diǎn)的極密度值分別為1.52和1.99,與其較低的超聲波波速一致。而P6和P13檢測(cè)點(diǎn)的極密度值分別為2.89和7.91,對(duì)應(yīng)較高的超聲波波速。
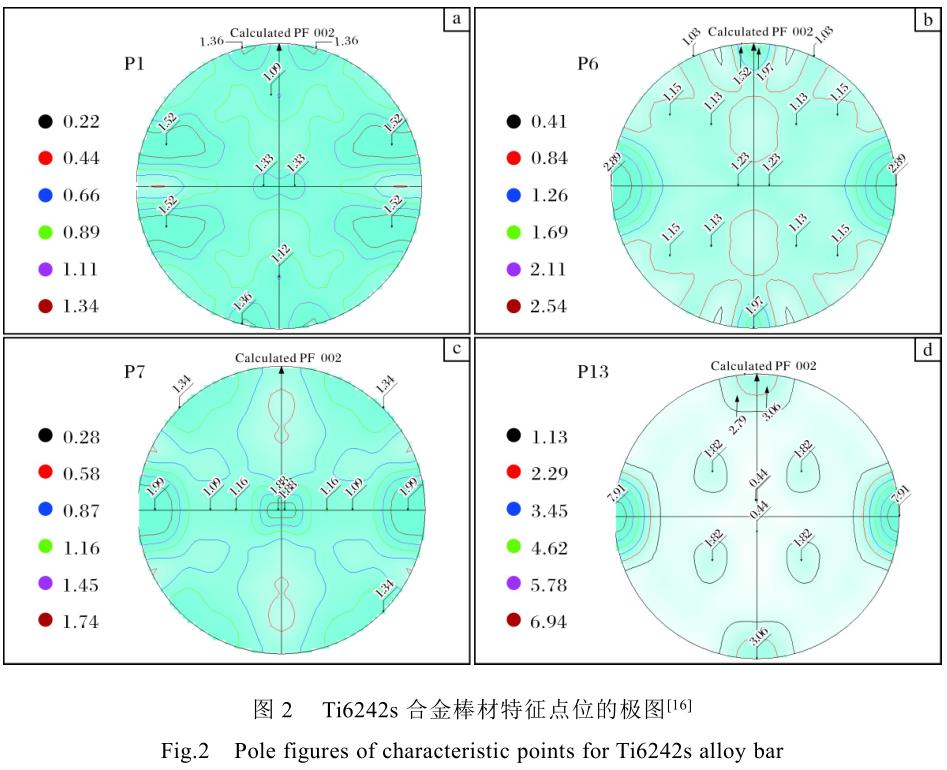
對(duì)于通過(guò)液壓機(jī)鍛造加工的大規(guī)格鈦合金棒材,由于變形速率較慢,壓力可以傳導(dǎo)至棒材內(nèi)部,變形往往集中在棒材心部(P13),造成心部的極密度值遠(yuǎn)大于其他部位。大規(guī)格棒材在最后使用模具歸圓的過(guò)程中,由于變形量很小,往往變形集中在次表面(P5-P7)附近。而棒材邊部受到溫降的影響,流變抗力增加,變形量相對(duì)較小。變形量的差異造成大規(guī)格棒材各處的極密度值差別較大,因此大規(guī)格鈦合金棒材的超聲波波速沿直徑方向呈現(xiàn)三峰結(jié)構(gòu)。
除了織構(gòu)會(huì)對(duì)鈦合金的超聲波波速產(chǎn)生影響,顯微組織也會(huì)對(duì)超聲波波速產(chǎn)生影響。鈦合金顯微組織的類型和形態(tài)與加工工藝以及熱處理制度有關(guān),顯微組織的變化會(huì)影響材料的彈性模量,進(jìn)而影響超聲波波速。
韓飛孝等[3]研究了TC4鈦合金軋制棒材的加工工藝和熱處理工藝對(duì)超聲波波速的影響。在940℃軋制的棒材,變形量由69.14%增加至92.89%時(shí),超聲波波速?gòu)?136m/s降至6093m/s;軋制溫度從900℃升高至980℃時(shí),超聲波波速?gòu)?110m/s提高到6162m/s。李運(yùn)等[4]研究了精鍛溫度、變形量及熱處理制度對(duì)Ti7Al4Mo合金棒材超聲波波速的影響。研究發(fā)現(xiàn),隨著變形溫度的升高,棒材初生α相含量逐漸降低,而超聲波波速逐漸增大。
2、鈦合金中超聲波雜波水平的影響因素
2.1超聲波在鈦合金中的傳播規(guī)律
超聲波從一種介質(zhì)傳播到另一種介質(zhì)時(shí),在兩種介質(zhì)的界面處會(huì)發(fā)生反射和透射。第一介質(zhì)和第二介質(zhì)界面處的聲強(qiáng)反射率R可以表示為:

式中,Z1和Z2分別為兩種介質(zhì)的聲阻抗。聲阻抗Z與介質(zhì)密度ρ和超聲波縱波波速c有關(guān),可以表示為:

其中,超聲波縱波波速又與材料的彈性模量密切相關(guān)。對(duì)于六方結(jié)構(gòu)鈦合金,彈性模量的各向異性導(dǎo)致不同取向區(qū)域(或晶粒)的波速和聲阻抗存在差異,進(jìn)而造成區(qū)域界面(或晶界)處發(fā)生發(fā)射,超聲探頭接收到的這些反射信號(hào)即顯示為雜波[5,9]。
另外,影響雜波水平的一個(gè)關(guān)鍵因素是反射界面的大小。對(duì)于鈦合金超聲檢測(cè)常用的探頭,頻率一般為5MHz或10MHz,其對(duì)應(yīng)的超聲波波長(zhǎng)分別為1.2mm和0.6mm。如果鈦合金的晶粒尺寸在幾十微米量級(jí),其晶界反射界面的尺寸遠(yuǎn)小于超聲波波長(zhǎng),界面處的反射很小,可以忽略不計(jì)。而當(dāng)晶粒大小與超聲波波長(zhǎng)在同一量級(jí)時(shí),界面處的反射增強(qiáng),超聲波雜波強(qiáng)度增大。
2.2鈦合金組織和織構(gòu)對(duì)超聲波雜波水平的影響
一般情況下,鈦合金經(jīng)過(guò)熱加工變形使晶粒細(xì)化后,超聲波雜波水平會(huì)得到改善。然而,在實(shí)際生產(chǎn)中,往往會(huì)出現(xiàn)隨著變形量的增加,雜波水平異常升高的現(xiàn)象,這與變形引起的晶粒形態(tài)和織構(gòu)變化有關(guān)。
Thompson等人[6]研究了Ti6246合金微觀組織對(duì)超聲波雜波水平的影響,并建立了通過(guò)超聲波雜波數(shù)據(jù)獲得材料品質(zhì)因數(shù)的模型。Li等人[11]研究了多晶材料中晶粒形狀和織構(gòu)與超聲波背散射的關(guān)系,建立了具有織構(gòu)化橢圓形晶粒的多晶材料超聲背散射模型。Humbert等人[9]研究了IMI834鈦合金盤件高雜波區(qū)(HBA)和低雜波區(qū)(LBA)的織構(gòu)。如圖3所示,在高雜波區(qū),六方晶粒的c軸沿餅材直徑方向排列的比例高達(dá)35%,這些相同取向的晶粒形成了一個(gè)晶格取向相同的晶粒群,稱之為“宏區(qū)”。當(dāng)超聲波穿過(guò)宏區(qū)時(shí),由于宏區(qū)內(nèi)各晶粒的聲阻抗基本一致,超聲波會(huì)將其視為一個(gè)“大型”晶粒,并在宏區(qū)的界面處發(fā)生反射,導(dǎo)致雜波強(qiáng)度增大。
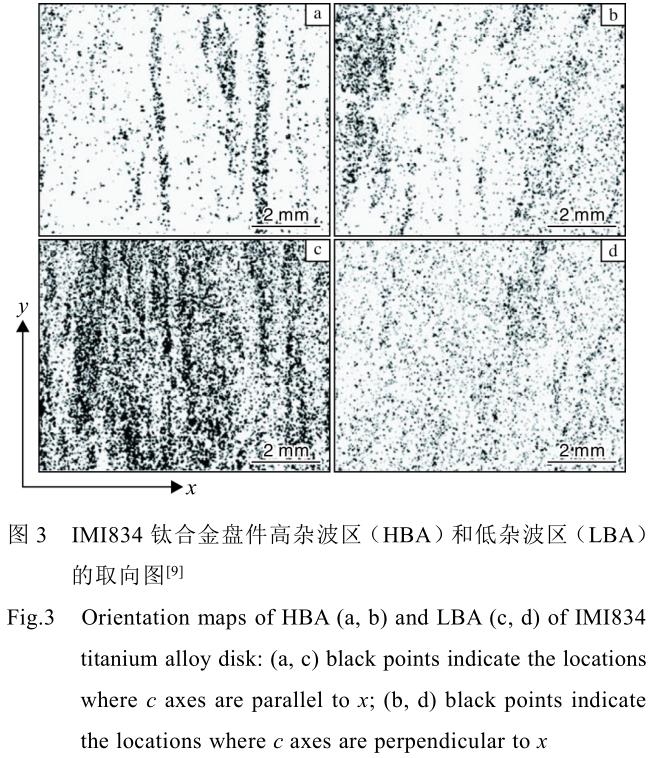
在鈦合金生產(chǎn)中,加工工藝–組織和織構(gòu)–超聲波雜波水平之間有著緊密的聯(lián)系。李磊等人[17]對(duì)葉片用小規(guī)格TC4鈦合金徑鍛棒材的組織和織構(gòu)進(jìn)行分析得到了棒材心部和邊部的反極圖(IPF圖),如圖4所示。從圖4可以看出,棒材邊部和心部的組織和織構(gòu)存在明顯差異。這是由徑鍛加工特殊的變形方式造成的。棒材徑鍛過(guò)程中,4個(gè)鍛錘高速往復(fù)錘擊棒材,棒材受到?jīng)_擊載荷快速變形。由于沖擊載荷主要作用于樣品邊部區(qū)域,且會(huì)產(chǎn)生切向應(yīng)力,邊部晶粒迅速破碎,并沿軸向被拉長(zhǎng),形成強(qiáng)烈的{0001}<1010>板織構(gòu)。心部區(qū)域的晶粒雖然也得到細(xì)化,但是錘擊產(chǎn)生的沖擊載荷不易傳導(dǎo)至心部,變形量相對(duì)邊部較小,晶粒尺寸也比邊部大。而且心部區(qū)域在各個(gè)方向的受力基本一致,因此形成了<1010>//軸向的絲織構(gòu)。
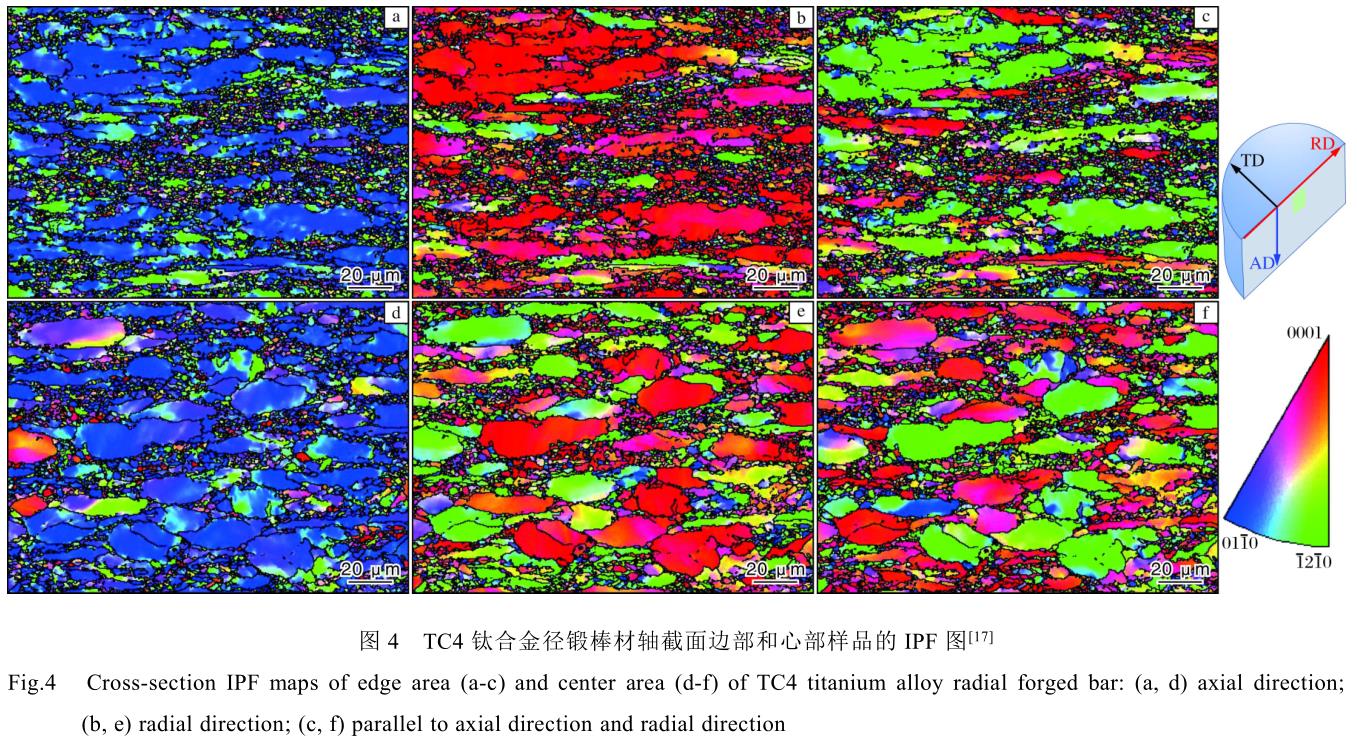
TC4鈦合金徑鍛棒材的這種梯度組織和織構(gòu)特征造成超聲波雜波的異常信號(hào)。圖5為TC4鈦合金徑鍛棒材水浸超聲波檢測(cè)的A掃圖,可以看出在22~30mm范圍內(nèi)(棒材R/2到周面區(qū)域)出現(xiàn)了雜波強(qiáng)度異常增大現(xiàn)象。
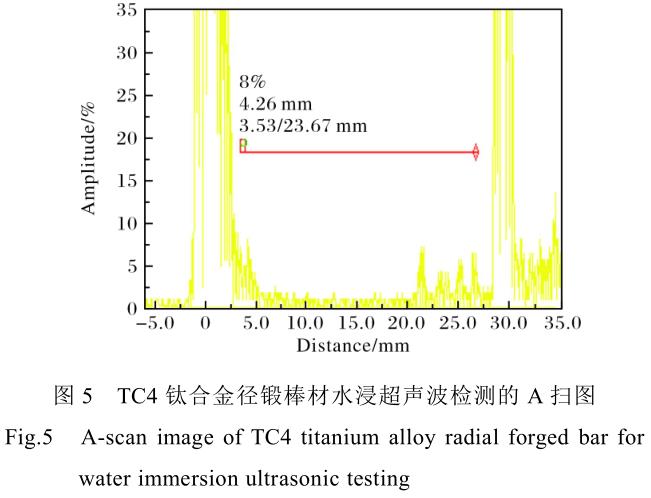
對(duì)于異常的超聲波雜波信號(hào),不僅需要分析材料的組織和織構(gòu),還需要結(jié)合材料加工的方式和工藝,才能理解其產(chǎn)生機(jī)理。該異常區(qū)域?qū)?yīng)棒材的邊部,其晶粒尺寸相對(duì)心部更加細(xì)小。雜波強(qiáng)度增加是由于邊部晶粒被拉長(zhǎng),以及強(qiáng)織構(gòu)導(dǎo)致的宏區(qū)效應(yīng),造成超聲波反射增強(qiáng),雜波水平超過(guò)指標(biāo)要求。通過(guò)增加徑鍛溫度、縮短徑鍛坯料長(zhǎng)度等方法可以優(yōu)化棒材的織構(gòu)分布,降低超聲波的雜波水平,滿足指標(biāo)要求[18]。
3、鈦合金中超聲波底波衰減的影響因素
引起超聲波底波衰減的主要原因有波束擴(kuò)散、介質(zhì)吸收和晶粒散射。擴(kuò)散衰減與鈦合金樣品探測(cè)方向的長(zhǎng)度有關(guān),超聲波的聲壓與長(zhǎng)度的平方根成反比,介質(zhì)吸收與質(zhì)點(diǎn)間的內(nèi)摩擦和熱傳導(dǎo)有關(guān)。散射衰減指超聲波在鈦合金中傳播時(shí),遇到聲阻抗不同的界面產(chǎn)生散亂反射而引起的衰減。散射衰減與鈦合金的組織和織構(gòu)密切相關(guān),一般情況下,晶粒粗大時(shí),散射衰減比較嚴(yán)重,被散射的聲波形成雜波造成信噪比下降,可能會(huì)淹沒(méi)缺陷信號(hào)[19-20]。
韓飛孝等人[18]研究了熱加工工藝對(duì)TC4鈦合金棒材組織和超聲波雜波的影響。對(duì)文獻(xiàn)[18]中西部超導(dǎo)材料科技股份有限公司在940℃通過(guò)徑鍛(1#)和軋制(2#)制備的φ30mmTC4鈦合金棒材的橫截面進(jìn)行超聲波底波強(qiáng)度C掃描和織構(gòu)檢測(cè),結(jié)果如圖6、圖7所示[17]。
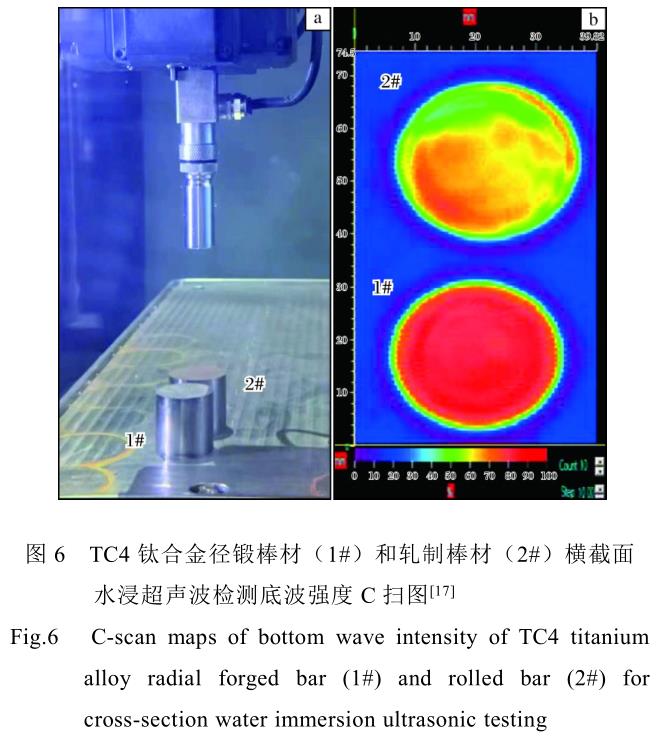
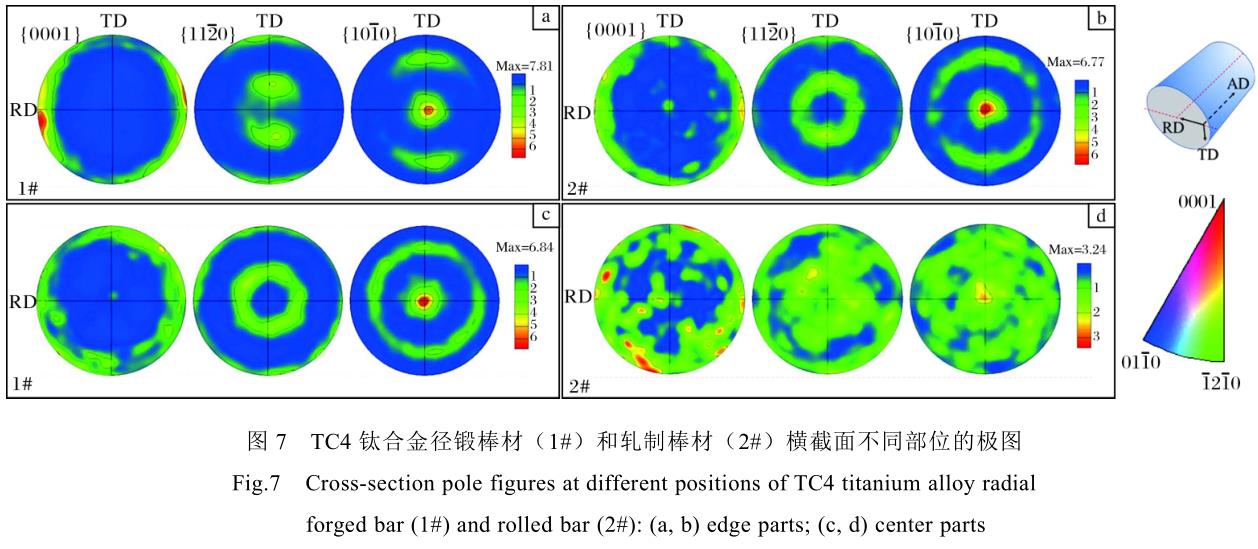
從圖6可見,徑鍛棒材的底波強(qiáng)度在各個(gè)方向基本一致,且變化較小;軋制棒材的底波強(qiáng)度出現(xiàn)了明顯的各向異性,且心部與邊部的強(qiáng)度相差較大。根據(jù)圖7中2種棒材邊部和心部的極圖可知,徑鍛棒材邊部與心部的極密度分別為7.81和6.84;軋制棒材邊部與心部的極密度分別為6.77和3.42。由此可見,在顯微組織相近的情況下,由于加工方式造成的TC4鈦合金棒材不同部位的織構(gòu)差異對(duì)超聲波的底波衰減有明顯的影響。
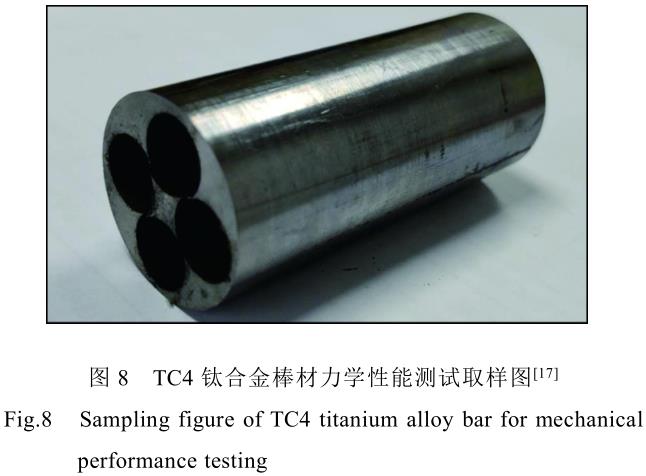
按圖8所示在TC4鈦合金徑鍛棒材和軋制棒材上沿軸向取樣進(jìn)行力學(xué)性能測(cè)試。徑鍛棒材抗拉強(qiáng)度和屈服強(qiáng)度的變異系數(shù)分別為0.24%和0.29%;而軋制棒材的變異系數(shù)分別為0.33%和0.49%。軋制棒材的力學(xué)性能波動(dòng)相對(duì)較大,這與其超聲波底波強(qiáng)度明顯的各向異性一致。
4、鈦合金超聲波檢測(cè)技術(shù)研究進(jìn)展
鈦合金的組織和織構(gòu)對(duì)其力學(xué)性能和疲勞性能有顯著影響[21-22]。鈦合金中的織構(gòu)宏區(qū),特別是包含高比例c軸與受力方向一致的α相宏區(qū),已經(jīng)被確認(rèn)為導(dǎo)致鈦合金零部件過(guò)早失效的疲勞損傷累積區(qū)。超聲波檢測(cè)作為一種無(wú)損檢測(cè)方法,成為鈦合金關(guān)鍵零部件織構(gòu)宏區(qū)檢測(cè)的重要手段,近年來(lái)超聲波織構(gòu)的檢測(cè)技術(shù)也取得了很多重要進(jìn)展。
Moreau等人[23]提出了一種基于超聲波波速波動(dòng)的空間自相關(guān)函數(shù)的無(wú)損檢測(cè)方法,能夠定量表征鈦合金宏區(qū)的大小。利用該方法檢測(cè)IMI834鈦合金中的織構(gòu)宏區(qū),其結(jié)果與EBSD的測(cè)試結(jié)果一致。Lan等人[24]通過(guò)理論計(jì)算和實(shí)驗(yàn)研究,提出了一種具有代表性的體積元方法,能夠檢測(cè)兩相結(jié)構(gòu)鈦合金織構(gòu)對(duì)超聲波波速的影響,進(jìn)而甄別織構(gòu)宏區(qū)。之后,Lan等人[25-26]又提出了一種利用共振超聲光譜(RUS)對(duì)織構(gòu)進(jìn)行無(wú)損評(píng)估的方法。將多晶區(qū)域的定向波速與其織構(gòu)建立聯(lián)系,并采用RUS通過(guò)測(cè)量彈性常數(shù)來(lái)獲得
波速數(shù)據(jù)以判定材料的織構(gòu)。Du[27]研究發(fā)現(xiàn),模式轉(zhuǎn)換超聲散射的振幅高度依賴于微觀組織的各向異性,并利用模式轉(zhuǎn)換超聲散射技術(shù)表征了Ti-6Al-4V合金坯料低散射和高散射區(qū)域的微觀組織。模式轉(zhuǎn)換超聲散射法提供了一種表征微觀組織各向異性的無(wú)損檢測(cè)方法,可作為質(zhì)量控制的無(wú)損檢測(cè)方式。
5、結(jié)語(yǔ)
鈦合金中超聲波的傳播受到密排六方結(jié)構(gòu)晶體彈性模量各向異性的影響,使得超聲波的波速、底波衰減以及超聲波雜波信號(hào)與鈦合金產(chǎn)品的組織和織構(gòu)密切相關(guān)。通過(guò)對(duì)超聲波信號(hào)的細(xì)致分析,能夠判斷鈦合金產(chǎn)品復(fù)雜的微觀結(jié)構(gòu)以及織構(gòu)特征,并結(jié)合鈦合金加工過(guò)程分析異常超聲波信號(hào)產(chǎn)生的原因,通過(guò)改進(jìn)加工工藝使其滿足鈦合金相關(guān)標(biāo)準(zhǔn)。近年來(lái)開發(fā)的鈦合金超聲波檢測(cè)技術(shù)有織構(gòu)宏區(qū)的定量表征方法、共振超聲光譜無(wú)損評(píng)估方法以及模式轉(zhuǎn)換超聲散射技術(shù)等,并已應(yīng)用于航空航天等領(lǐng)域鈦合金零部件的無(wú)損檢測(cè)。
參考文獻(xiàn)References
[1] 趙永慶, 葛鵬, 辛社偉. 近五年鈦合金材料研發(fā)進(jìn)展[J]. 中國(guó)材料進(jìn)展, 2020, 39(Z1): 527-534.
[2] 趙秦陽(yáng), 陳永楠, 徐義庫(kù), 等. 鈦合金材料低成本化制備技術(shù) 進(jìn) 展 與 展 望 [J]. 中 國(guó) 有 色 金 屬 學(xué) 報(bào) , 2021, 31(11):3127-3140.
[3] 韓飛孝, 孫小平, 樓美琪, 等. 軋制和熱處理工藝對(duì) TC4 鈦合 金棒 材 超 聲聲 速 的影 響 [J]. 鈦 工業(yè) 進(jìn) 展, 2023, 40(6):16-21.
[4] 李運(yùn), 韓飛孝, 秦立東, 等. 加工工藝對(duì) Ti7Al4Mo 合金棒材 組 織 性 能 和 超 聲 聲 速 的 影 響 [J]. 鈦 工 業(yè) 進(jìn) 展 , 2022,39(6): 18-23.
[5] 李華, 馬英杰, 邱建科, 等. TC4 鈦合金顯微組織對(duì)超聲波探 傷 雜 波 水 平 的 影 響 [J]. 稀 有 金 屬 材 料 與 工 程 , 2013,42(9): 1859-1863.
[6] Thompson R B, Margetan F J, Rose J H, et al. Influence of microstructure on ultrasonic backscattering noise in titanium alloys[J]. Nondestructive Testing and Evaluation, 1992, 8-9(1-6):485-495.
[7] Gigliotti M F X, Bewlay B P, Deaton J B, et al.Microstructure-ultrasonic inspectability relationships in Ti6242: signal-to-noise in fine-grain-processed Ti6242[J].Metallurgical and Materials Transactions A, 2000, 31:2119-2125.
[8] Wu J, Wang L, Liu X, et al. Evolution of microstructure and microtexture in Ti-2A1-2.5Zr during one pass cold pilgering[J]. Rare Metal Materials and Engineering, 2022,51(4): 1145-1151.
[9] Humbert M, Moreau A, Uta E, et al. Analysis of backscattered ultrasound amplitude of Ti-5.8Al-4Sn-3.5Zr-0.7Nb-0.5Mo-0.3Si samples in term of their microstructures and local textures[J]. Acta Materialia, 2009, 57: 708-714.
[10] Lobkis O I, Yang L, Li J, et al. Ultrasonic backscattering in polycrystals with elongated single phase and duplex microstructures[J]. Ultrasonics, 2012, 52 (6): 694-705.
[11] Li J, Yang L, Rokhlin S I. Effect of texture and grain shape on ultrasonic backscattering in polycrystals[J]. Ultrasonics, 2014, 54(7): 1789-1803.
[12] Baelde A, Laurent J, Millien P, et al. Effect of microstructural elongation on backscattered field: Intensity measurement and multiple scattering estimation with alinear transducer array[J]. Ultrasonics, 2018, 82: 379-389.
[13] Kube C M, Arguelles A P, Turner J A. Ultrasonic backscatter from elongated grains using line focused ultrasound[J].Ultrasonics, 2018, 82: 79-83.
[14] Li X B, Fu Y D, Zhang F, et al. Detecting small flaws in two-phase Ti-6Al-4V with rough surfaces[J]. Ultrasonics, 2020, 106: 106128.
[15] Fisher E S, Renken C J. Single-crystal elastic moduli and the hcp→bcc transformation in Ti, Zr, and Hf[J]. Physical Review, 1964, 135: A482-A494.
[16] Zheng G M, Mao X N, Li L, et al. The variation of microstructures, textures and mechanical properties from edge to center in cross section of Ti6242s titanium alloy[J].Vacuum, 2019, 160: 81-88.
[17] 李磊, 韓飛孝, 周敏, 等. 葉片用小規(guī)格 TC4 棒材的組織和 織 構(gòu) 研 究 [J]. 稀 有 金 屬 材 料 與 工 程 , 2023, 52(11):3909-3914.
[18] 韓飛孝, 孫小平, 鄭念慶, 等. 熱加工工藝對(duì)葉片用 TC4鈦 合 金 棒 材 組 織 與 性 能 的 影 響 [J]. 鈦 工 業(yè) 進(jìn) 展 , 2022,39(6): 7-12.
[19] Blodgett M P, Eylon D. The influence of texture and phase distortion on ultrasonic attenuation in Ti-6Al-4V[J]. Journal of Nondestructive Evaluation, 2001 20(1): 1-15.
[20] Bhattacharjee A, Pilchak A L, Lobkis O I, et al. Correlating ultrasonic attenuation and microtexture in a near-alpha titanium alloy[J]. Metallurgical and Materials Transactions A, 2011, 42: 2358-2372.
[21] Warwick J L W, Coakley J, Raghunathan S L, et al. Effect of texture on load partitioning in Ti-6Al-4V[J]. Acta Materialia,2012, 60: 4117-4127.
[22] Liu Y, Dunne F P E. The mechanistic link between macrozones and dwell fatigue in titanium alloys[J]. International Journal of Fatigue, 2021, 142: 105971.
[23] Moreau A, Toubal L, Bocher P, et al. Evaluation of macrozone dimensions by ultrasound and EBSD techniques[J]. Materials Characterization,2013,75:115-128.
[24] Lan B, Lowe M, Dunne F P E. Experimental and computational studies of ultrasound wave propagation in hexagonal close-packed polycrystals for texture detection[J].Acta Materialia, 2014, 63: 107-122.
[25] Lan B, Carpenter M A, Gan W, et al. Rapid measurement of volumetric texture using resonant ultrasound spectroscopy[J]. Scripta Materialia, 2018, 157: 44-48.
[26] Lan B, Britton T B, Jun T S, et al. Direct volumetric measurement of crystallographic texture using acoustic waves[J]. Acta Materialia, 2018, 159: 384-394.
[27] Du H L. Characterization of microstructural anisotropy using the mode-converted ultrasonic scattering in titanium alloy[J].Ultrasonics, 2022, 119: 106633.
相關(guān)鏈接