鈦合金管具有耐腐蝕性強(qiáng)、比強(qiáng)度高等優(yōu)點(diǎn),廣泛應(yīng)用于化工、海洋工程、核電、艦船及航空航天領(lǐng)域[1-3]。目前鈦合金管一般通過深孔鉆鏜孔工藝或斜軋穿孔及軋制獲得。鉆鏜孔工藝材料利用率低,提高了加工成本,斜軋穿孔及軋制設(shè)備復(fù)雜,周期長,成品率低,且僅應(yīng)用于低強(qiáng)度鈦合金管的加工[4-5]。鈦合金深孔環(huán)形套料鉆削工藝可以有效克服以上加工工藝的缺點(diǎn),但由于加工空間較小、切屑形態(tài)不好等原因,鈦合金深孔環(huán)形套料鉆削時(shí)易引發(fā)堵屑現(xiàn)象。優(yōu)化切削液性能是保證排屑順暢的關(guān)鍵技術(shù)之一。切削液的選用直接影響切削力、切削形態(tài)和刀具磨損,導(dǎo)致排屑性能差異較大[6-7]。諸多學(xué)者分析了切削液對切削過程中材料切削特性的影響,黃景山等[8]選用不同密度的切削液進(jìn)行高強(qiáng)度鋼的切削試驗(yàn),試驗(yàn)表明恰當(dāng)密度的切削液可以有效降低刀具表面的磨損;倪敬等[9]選用不同配比的切削液進(jìn)行霧化拉伸試驗(yàn),試驗(yàn)表明添加劑加入切削液以降低拉削負(fù)載時(shí)并非越多越好,而是存在最佳值;劉騰飛等[10]選用了不同的切削液進(jìn)行了TC4鈦合金切削試驗(yàn),試驗(yàn)表明不同的切削液對于降低切削力、減少刀具磨損有很大的差異表現(xiàn);龍軍城等[11]研究了深孔加工中切削液對加工質(zhì)量的影響,結(jié)果表明切削液選擇不合適將會導(dǎo)致切屑變長,導(dǎo)致堵屑、刀具磨損,進(jìn)而影響加工效率。上述學(xué)者們通過試驗(yàn)研究證明了切削液選用恰當(dāng)?shù)拿芏取⒊煞值瓤梢杂行Ы档图庸ぶ械毒吣p、降低切削力、減少堵屑現(xiàn)象等。基于Fluent等流體軟件進(jìn)行仿真模擬為提高加工中切削液排屑性能的研究提供了新途徑。通過仿真分析可以獲得實(shí)際加工中不易獲得的參數(shù)并提高排屑能力[12-13]。OezkayaE等[14]通過仿真分析切削液黏度對螺旋深孔鉆削中湍流動能的影響,證明恰當(dāng)?shù)酿ざ群颓邢饕簤毫τ欣跀嗔鲃幽艿目刂啤YR彩彩等[15]通過通過仿真分析獲得鉆頭前后壓強(qiáng)差的降低有利于減少湍流強(qiáng)度。為此,本文以TC4鈦合金棒材為研究對象,基于Fluent軟件,采用響應(yīng)面分析法進(jìn)行切削液參數(shù)優(yōu)化,以切削液黏度、流量和密度為變量,以第一刀齒的斷屑槽壓力和湍流動能為優(yōu)化目標(biāo),優(yōu)化TC4鈦合金深孔套料鉆削的排屑性能,并開展深孔環(huán)形套料鉆削試驗(yàn)驗(yàn)證。
1、鉆削系統(tǒng)及有限元模型的建立
1.1內(nèi)排屑深孔套料鉆削
內(nèi)排屑深孔套料鉆削系統(tǒng)如圖1a所示,切削液通過授油器進(jìn)入內(nèi)腔,經(jīng)過工件內(nèi)壁和鉆桿外壁之間的空隙,流入套料鉆刀齒處,并攜帶切削從刀桿內(nèi)壁和工件芯桿之間的空隙流出。套料鉆選用四齒深孔套料鉆,如圖1b所示,四齒沿徑向方向向內(nèi)分布。由于刀齒分布為均勻向內(nèi)布置,研究位于外側(cè)的第一刀齒的響應(yīng)情況后,可推斷剩余三齒變化。因此,本文主要研究第一刀齒的斷屑槽壓力及湍流動能。

1.2有限元模型建立
基于Fluent仿真軟件,建立套料鉆和工件的流體域模型。其中流速根據(jù)切削液的流量進(jìn)行換算可得。采用湍流強(qiáng)度和水力直徑進(jìn)行湍流設(shè)置,根據(jù)計(jì)算,設(shè)置水力半徑為0.186m,湍流強(qiáng)度默認(rèn)。為了減小流體分析的難度和提高試驗(yàn)的準(zhǔn)確度,將流體介質(zhì)選成液態(tài)水,將其材料屬性黏度和密度設(shè)置為優(yōu)化參數(shù)。壁面參數(shù)根據(jù)試驗(yàn)安排設(shè)置,設(shè)置不同接觸面的材料屬性,見表1。湍流模型選擇標(biāo)準(zhǔn)Standardk模型,壁面函數(shù)采用標(biāo)準(zhǔn)壁面函數(shù)SWF),采用Coupled算法求解,求解精度均采用二階迎風(fēng),各項(xiàng)殘差設(shè)置為1×10-5。

2、響應(yīng)曲面法優(yōu)化切削液參數(shù)
2.1仿真試驗(yàn)方案的確定
根據(jù)加工經(jīng)驗(yàn)和參考文獻(xiàn)[16-18]選取試驗(yàn)中變量及各個(gè)變量的取值范圍:切削液密度A取值范圍為998.2~1100kg/m3,切削液黏度B取值范圍為0.001003~0.029000kg/(m.s),切削液流量C取值范圍為125~180L/min。響應(yīng)變量為第一刀齒斷屑槽壓力和斷屑槽湍流動能。通過BBD設(shè)計(jì)三因素三水平兩響應(yīng)試驗(yàn),方案及試驗(yàn)結(jié)果見表2。
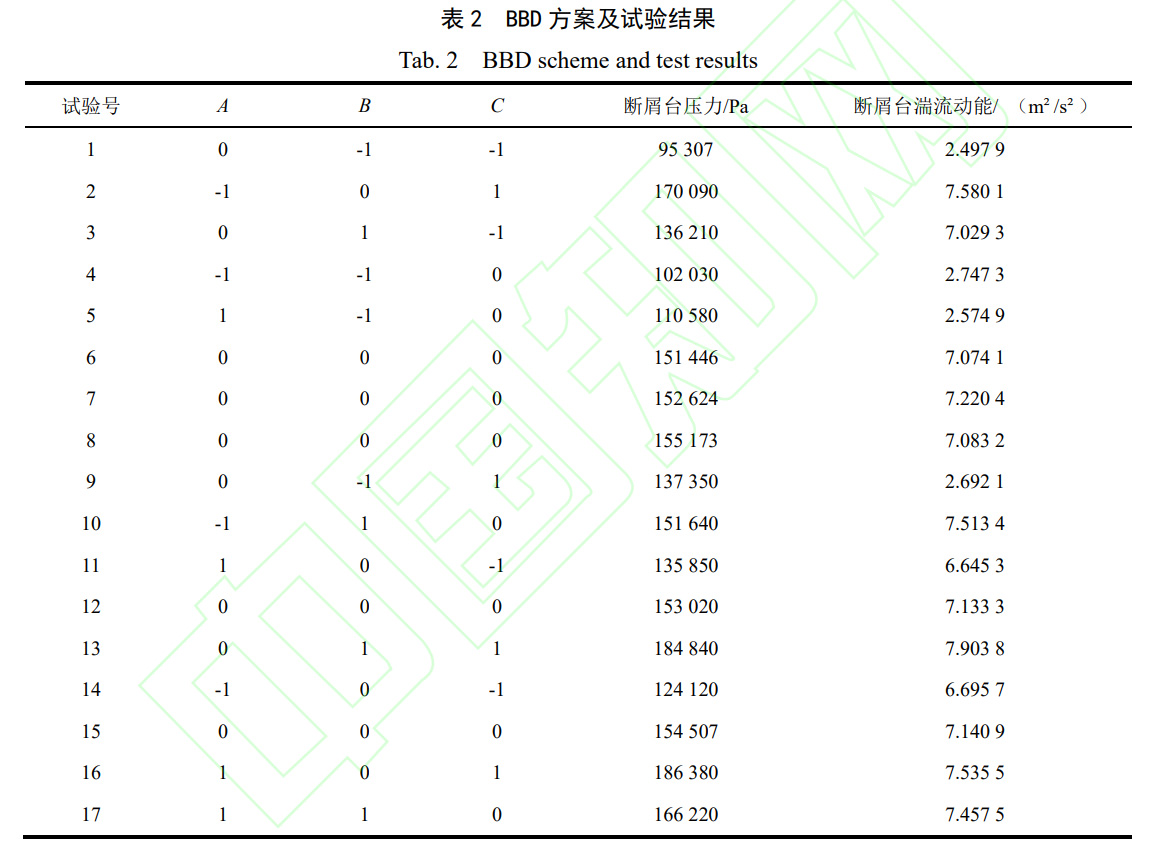
2.2試驗(yàn)結(jié)果分析
在軟件中設(shè)置擬合2次得出最佳結(jié)果,見表3,不需要引入更高次。對表3分析可知,此回歸模型中P<0.0001,表明此模型表現(xiàn)極顯著;失擬項(xiàng)的P值0.0526大于0.05,表明失擬水平不顯著;校正系數(shù)R2為0.9953,表明該模型能較好地反映第一刀齒斷屑槽壓力與切削液參數(shù)之間的關(guān)系。模型變異系數(shù)Cv為1.87%,說明試驗(yàn)相關(guān)操作是合理可信的。因此,上述擬合模型可以對第一刀齒斷屑槽進(jìn)行預(yù)測。
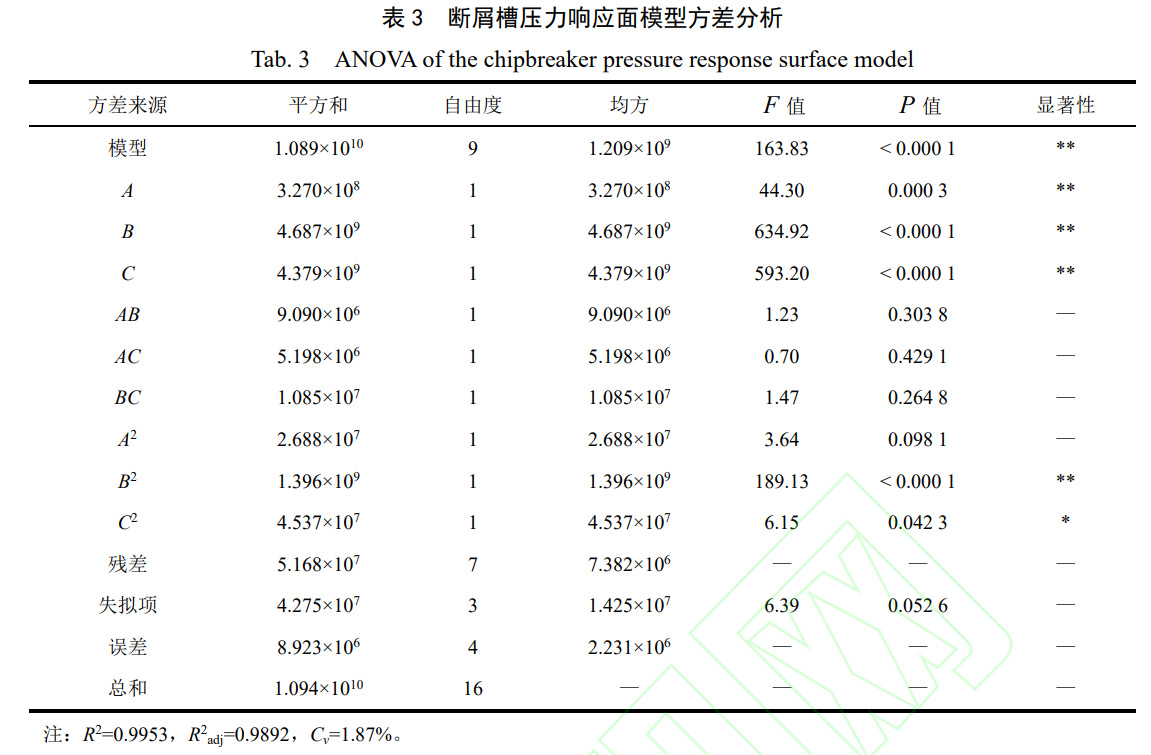
在表3分析結(jié)果中比較切削液三因素的F值:切削液黏度B>切削液流量C>切削液密度A,說明切削液黏度對湍流動能的影響最大,切削液流量影響次之,切削液密度影響較小,并且切削液三因素的P值均小于0.01,表現(xiàn)為高度顯著。
斷屑槽湍流動能響應(yīng)面模型方差分析見表4,可知此回歸模型中P<0.0001,表明此模型表現(xiàn)極顯著;失擬項(xiàng)的P值0.0521大于0.05,表明失擬水平不顯著;校正系數(shù)R2為0.9988,表明該模型能較好地反映湍流動能與切削液參數(shù)之間的關(guān)系。模型變異系數(shù)Cv=1.73%,說明試驗(yàn)相關(guān)操作是合理可信的。因此,上述擬合模型可以對湍流動能進(jìn)行預(yù)測。在表4分析結(jié)果中比較切削液三因素的F值:切削液黏度B>切削液流量C>切削液密度A,說明切削液黏度對湍流動能的影響最大,切削液流量影響次之,切削液密度影響較小,除切削液密度P>0.05,表現(xiàn)為不顯著,其余兩切削液參數(shù)P值均小于0.01,表現(xiàn)為高度顯著。
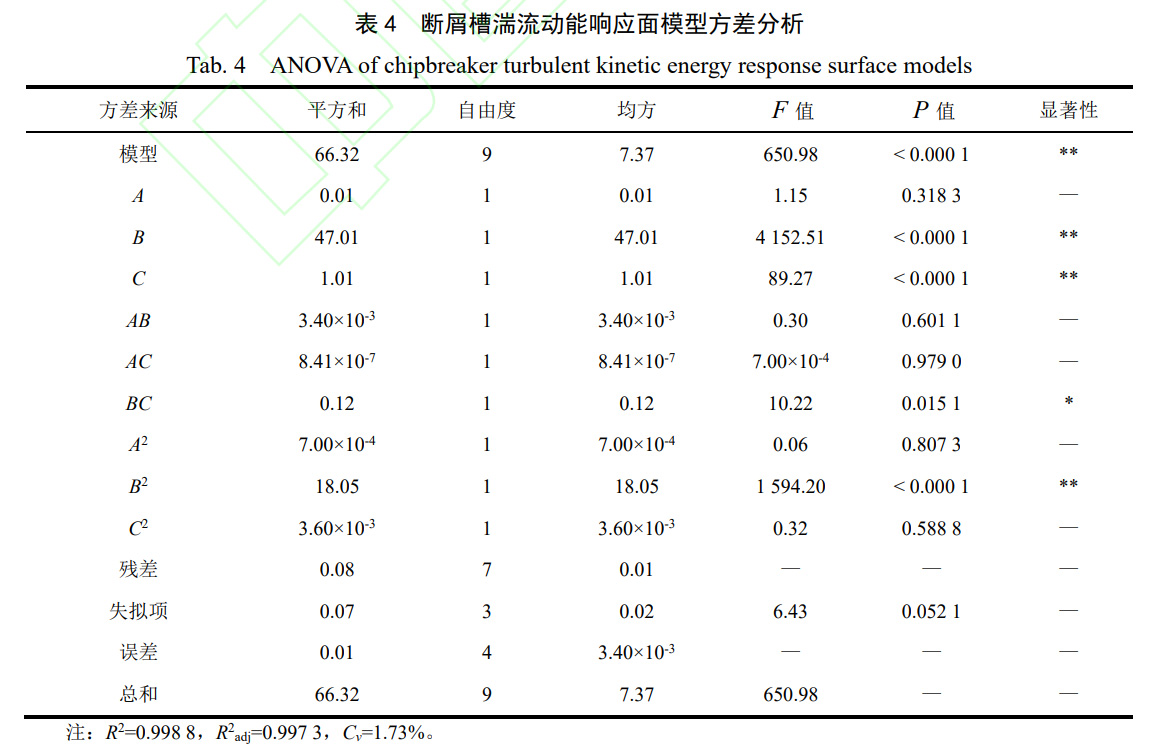
由圖2a可以看出:切削液密度和切削液流量與斷屑槽壓力均為線性正相關(guān)關(guān)系,切削液流量對斷屑槽壓力的影響更為顯著,切削液黏度對斷屑槽壓力的影響呈左增右減的弧線變化趨勢。交互作用方差分析中PBC(0.2648)<PAB(0.3038)<PAC(0.4291),即在多因素交互作用中切削液黏度和切削液流量對斷屑槽壓力的交互作用影響最顯著,切削液密度和切削液黏度的交互作用影響次之,切削液密度與切削液流量交互作用的影響最小。圖2b和圖2c取切削液黏度和切削液流量的交互影響分析,響應(yīng)面的傾斜度較高,坡度較為陡峭。當(dāng)黏度水平較低時(shí),流量的增加對斷屑槽壓力的影響不顯著,當(dāng)黏度水平較高時(shí),流量的增加使得斷屑槽壓力顯著增大,而黏度水平最高時(shí),流量水平的增加使得斷屑槽壓力變化的幅度略有降低。這是由于第一刀齒位于套料鉆刀具最外側(cè),根據(jù)管內(nèi)流體的流動特性,當(dāng)采用內(nèi)排屑的方式時(shí),切削液從授油器進(jìn)入鉆桿外壁與工件孔壁的空隙(即進(jìn)油間隙)有限,流體黏度是流體流動阻力的量度,黏度的增大,使得切削液作用在斷屑槽上的流體內(nèi)阻增大,即作用在同一處的流體量變大,導(dǎo)致了流體作用于斷屑槽的流體量增大,在斷屑槽作用面積不變的情況下,此處的壓力隨之增大,但隨著黏度增大,連續(xù)進(jìn)入內(nèi)腔的切削液摩擦著前面的切削液,變相的減小了斷屑臺上的流體量,減小了斷屑槽上切削液的作用力。
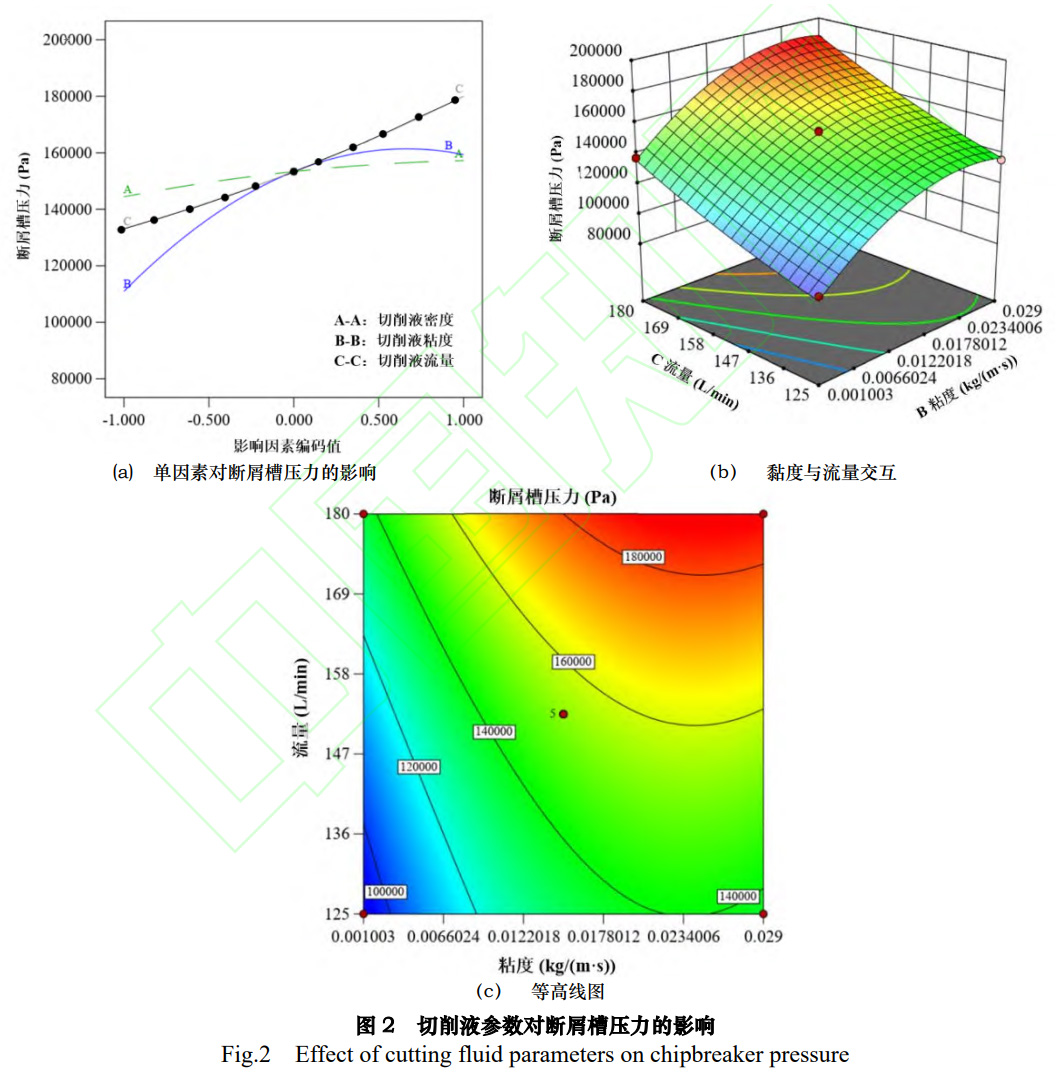
由圖3a可以看出,切削液密度及切削液流量與斷屑槽湍流動能均為線性正相關(guān)關(guān)系,其中切削液密度對湍流動能的影響較小,切削液黏度呈陡峭的弧度變化趨勢,并呈左增右減的趨勢。交互作用方差分析中PBC(0.0151)<PAB(0.6011)<PAC(0.9790),即在多因素交互作用中,切削液黏度和切削液流量對斷屑槽湍流動能的交互作用影響最顯著,切削液密度和切削液黏度的交互作用影響次之,切削液密度與切削液流量交互作用的影響最小。圖3b和圖3c取切削液黏度和切削液流量的交互影響分析,可以看出流量水平較低時(shí),隨著黏度的增加,湍流動能先增大后減小,而當(dāng)流量水平較高時(shí),黏度的增加使得湍流動能增加。這是由于黏度的增大,切削液之間的內(nèi)摩擦力加劇,而湍流動能是描述流體穩(wěn)定性的度量,它表現(xiàn)了流體維持湍流或發(fā)展成湍流的能力,這股流動阻力的變大,使得流體運(yùn)動不穩(wěn)定,這也產(chǎn)生了更大的湍流動能,但黏度繼續(xù)增大,作用在同一處流體量變大,變相地使其內(nèi)部的間距變大,反而減小了流動阻力,即湍流動能下降。當(dāng)流量足夠大時(shí),黏度增加引起的阻力使得湍流動能先增大后趨于穩(wěn)定。
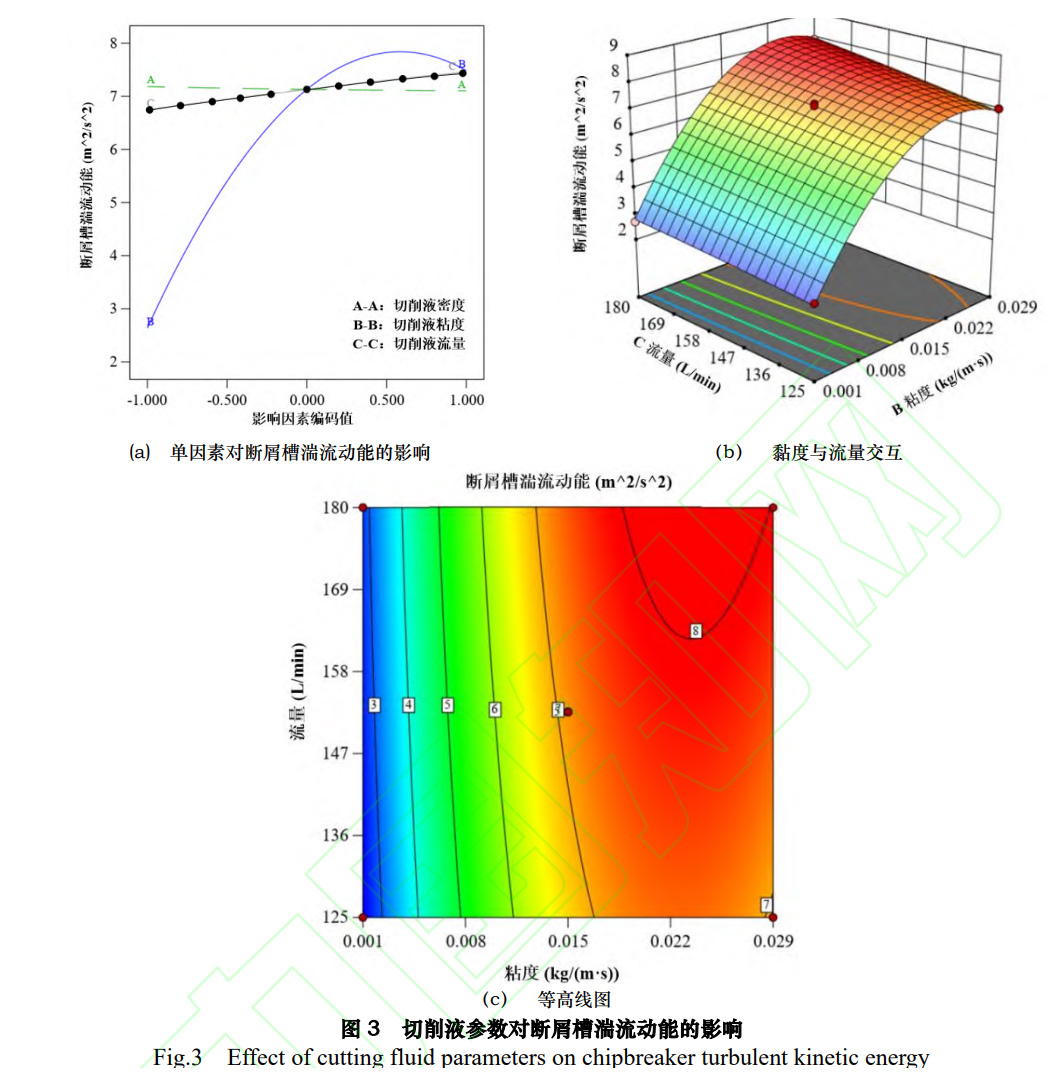
綜上所述,為了使得斷屑槽壓力增大并且降低斷屑槽湍流動能,則需要滿足:
(1)適當(dāng)增加切削液黏度;
(2)在套料鉆流域空間允許的前提下,盡量提高流量的取值;
(3)在保證添加劑不析出切削液的前提下,盡量提高切削液密度。
2.3最佳參數(shù)的確定
通過BBD設(shè)計(jì)的三因素三水平兩響應(yīng)試驗(yàn)的分析結(jié)果,剔除顯著性概率大于0.05的因素,包括第一刀齒斷屑槽壓力響應(yīng)面分析結(jié)果中的AB、AC、BC、A2,湍流動能響應(yīng)面分析結(jié)果中的A、AB、AC、A2、C2,最后可得出第一刀齒斷屑槽壓力Y1和湍流動能Y2關(guān)于A(切削液密度)、B(切削液黏度)、C(切削液流量)的多元非線性回歸方程。回歸模型分別為圖4所示為模型預(yù)測值與試驗(yàn)值的關(guān)系對應(yīng)圖,理論上所有的試驗(yàn)值都應(yīng)該在傾角為45°的直線上,試驗(yàn)值與理論值存在一定的偏差,點(diǎn)越靠近直線說明預(yù)測值與試驗(yàn)值越接近,模型的可信程度越高。圖4中大部分點(diǎn)都與理論值十分接近,說明關(guān)于第一刀齒斷屑槽壓力和湍流動能的2個(gè)預(yù)測模型能有效地解釋切削液三因素的變化關(guān)系,具有較高的準(zhǔn)確性。
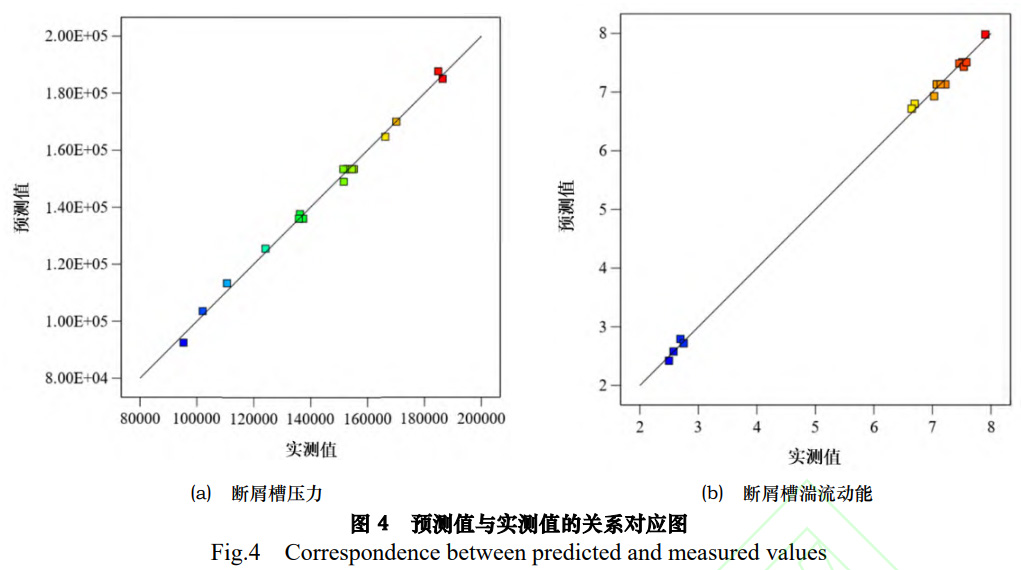
通過Design-expert軟件自動尋優(yōu)得到切削液的最優(yōu)參數(shù):密度1100kg/m3,黏度0.002kg/(m.s),流量180L/min。采用優(yōu)化后切削液進(jìn)行深孔環(huán)形套料,第一刀齒斷屑槽壓力為141816Pa,第一刀齒湍流動能為2.986m2/s2。在相同情況下,對比試驗(yàn)組(第16組),第一刀齒斷屑臺壓力變小,減小了23.9%;對于湍流動能來說,第一刀齒斷屑槽湍流動能減少了60.37%。壓力的相近表明排屑力的變化穩(wěn)定,更低的湍流動能代表排屑時(shí)的穩(wěn)定和較小的流體阻力。
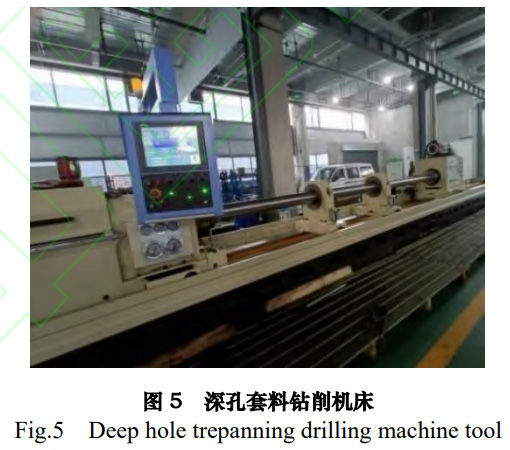
2.4試驗(yàn)驗(yàn)證
試驗(yàn)在深孔套料機(jī)床上展開,根據(jù)最優(yōu)參數(shù)結(jié)果和實(shí)際切削液的性能,將前期試驗(yàn)加工的切削液進(jìn)行合適配比,達(dá)到接近流體仿真的切削液成分,并采用該切削液進(jìn)行深孔環(huán)形套料鉆削。對照組采用表2中16組的切削液參數(shù)。由于目前無法直接測量第一刀齒斷屑臺壓力和湍流能,通過間接對比切屑形態(tài)和刀具磨損來分析優(yōu)化后的切削液對排屑性能的影響。
對照組和優(yōu)化組第一刀齒所獲得的切屑形態(tài),如圖6所示。第一刀齒以螺旋長屑為主。第一刀齒位于套料鉆最外側(cè),相對其他三個(gè)刀齒來說,切削刃切削半徑最大,切削速度最大,此時(shí)切屑上下面受力不均在厚度方向上產(chǎn)生卷曲,在斷屑槽上附加變形,切屑在彎矩作用下在變形,成為螺旋長屑。優(yōu)化組所獲得的切屑螺旋圈數(shù)減少,由三到五圈減少到一到兩圈,切屑長度至少減少一半。分析對照組和優(yōu)化組的切屑形態(tài),表明了優(yōu)化后的切削液可以顯著改善切屑形態(tài)。
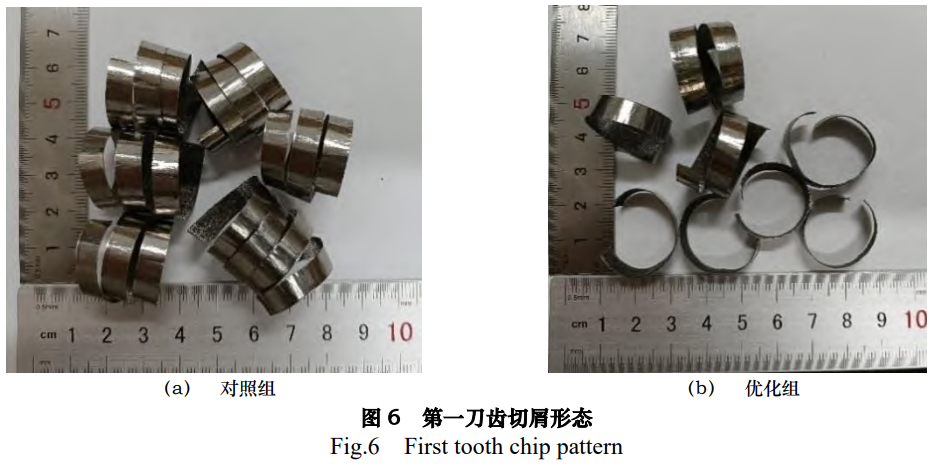
3、結(jié)語
(1)影響第一刀齒斷屑槽壓力和斷屑槽湍流動能的因素由大到小依次是切削液黏度、切削液流量和切削液密度。在多因素交互作用中切削液黏度和切削液流量對斷屑槽壓力及斷屑槽湍流動能的交互作用影響最顯著。
(2)通過仿真分析獲得切削液的最優(yōu)參數(shù)組合為密度1100kg/m3,黏度0.002kg/(m.s),流量180L/min。與對比組中第一刀齒斷屑槽壓力和湍流動能相比較,切削液優(yōu)化組獲得的第一刀齒斷屑臺壓力減小23.9%,湍流動能減少了60.37%,物理試驗(yàn)證明獲得的切屑形態(tài)長度明顯減小。
參考文獻(xiàn)
[1]張望成,魯蓉蓉,曾憲山.核電熱交換器用耐蝕鈦焊管制備工藝研究[J].鈦工業(yè)進(jìn)展,2021,38(4):34-37.
[2]周佳宇,哈軍,鈦合金材料在艦船管系上的應(yīng)用[J].材料開發(fā)與應(yīng)用,2006(6):40-42.
[3]張旺峰,張暉,顏孟奇,等.飛機(jī)液壓系統(tǒng)用 TA18 鈦合金管材性能特殊性研究[J].鈦工業(yè)進(jìn)展,2018,35(4):22-25.
[4]韓曉蘭,劉戰(zhàn)鋒.大孔徑鈦合金管深孔套料鉆削技術(shù)及應(yīng)用[J].重型機(jī)械,2022(6):48-52,58.
[5]劉行,姜增輝,邵忠偉,等.正交車銑大直徑鈦合金無縫管徑向切削力的研究[J].制造技術(shù)與機(jī)床,2024(7):80-84.
[6] Ma J, Mohammadi J, Zhou Y, et al. An investigation into cutting fluid additives performance during machining processing of Ti-6Al-4V[J]. The International Journal of Advanced Manufacturing Technology, 2021,112: 977-987.
[7]馮亞洲,黃帥澎,劉雁蜀,等.TA15 鈦合金深孔鉆削試驗(yàn)研究[J].制造技術(shù)與機(jī)床,2022(2):39-42.
[8]黃景山,劉國亮,孫浩,等.C60 納米粒子切削液對15Cr14Co12Mo5Ni2WA 齒輪鋼切削特性的影響研究[J].機(jī)械工程學(xué) 報(bào),2023,59(23):358-371.
[9]倪敬,劉曉帆,何利華,等.含添加劑蓖麻油切削液的拉削加工性能研究[J].中國機(jī)械工程,2019,30(23):2849-2856.
[10]劉騰飛,王宇,王聿禹,等.高潤滑性鈦合金切削液的制備及加工驗(yàn)證[J].潤滑與密封,2022,47(9):179-184.
[11]龍軍城,榮強(qiáng),張文,等.深孔加工中冷卻潤滑液的作用分析[J].工具技術(shù),2019,53(3):91-93.
[12]董偉康.深孔加工負(fù)壓排屑裝置結(jié)構(gòu)優(yōu)化設(shè)計(jì)[D].太原:中北大學(xué),2019.
[13]高琳,沈興全,陳振亞,等.基于 Fluent 冷卻排屑應(yīng)用的深孔槍鉆優(yōu)化設(shè)計(jì)[J].工具技術(shù),2018,52(2):57-60.
[14]Oezkaya E, Michel S,Biermann D. Experimental and computational analysis of the coolant distribution considering the viscosity of the cutting fluid during machining with helical deep hole drills[J]. Advances in Mavufacturing,2022,10(2):235–249.
[15] 賀彩彩, 董振, 魏斌, 等. BTA 深孔鉆射流孔參數(shù)的優(yōu)化與仿真[J].工具技術(shù), 2020, 54(1): 63-66. [16]仲為武.切削液冷卻條件下傳熱參數(shù)對切削熱傳輸?shù)挠绊慬J].制造技術(shù)與機(jī)床,2014(10):98-101.
[17]李薇,鄭光明,丁峰,等.清潔可持續(xù)切削及工藝參數(shù)多目標(biāo)優(yōu)化研究進(jìn)展[J].制造技術(shù)與機(jī)床,2024(9):79-85. [18]馮伯華,欒志強(qiáng),張若沖,等.電滲效應(yīng)對水基切削液在刀-屑界面滲透潤滑影響機(jī)理的實(shí)驗(yàn)研究[J].機(jī)械工程學(xué) 報(bào),2023,59(9):320-334.
第一作者/通信作者:韓曉蘭,女,1987 年生,博士,講師,主要研究方向?yàn)殡y加工材 料的深孔加工、設(shè)備成型一體化。E-mail:hanxiaolang007@163.com
相關(guān)鏈接